Der geringe Fertigungsaufwand und eine einfache Montage eröffnen gerändelten Kegelpressverbindungen ein weites Einsatzgebiet im Bereich der wieder lösbaren Welle-Nabe-Verbindungen. Erste am Institut für Konstruktionstechnik und Technisches Design (IKTD) durchgeführte Arbeiten zu gerändelten Kegelpress-verbindungen zeigen jedoch, dass auf Basis des Stands der Technik eine sichere Auslegung nicht möglich ist. Dies deckt sich mit Praxiserfahrungen, wonach trotz Auslegung nach gängigen Normen ein selbstständiges Lösen der Verbindung beobachtet wird.
Während des Aufpressens einer weichen Nabe auf einen härteren Kegelrändel drücken sich die Rändelstollen der Welle in das Nabenmaterial ein und bilden so eine formschlüssige Verbindung zwischen den beiden Fügepartnern. Dieser rein elastisch-plastische Fügevorgang unterscheidet sich grundsätzlich von dem zylindrischer Rändel-Pressverbindungen, bei denen die Nabe entlang der gesamten wirksamen Länge über das Rändelprofil der Welle gepresst wird. Hierbei können spanabhebende Furchungsvorgänge auftreten, welche bei kegelförmigen Geometrien unterbleiben. Bei Belastung der Verbindung mit äußeren Lasten treten in der Fuge Relativbewegungen auf, die zu einem Verlust der Vorspannung des axialen Sicherungselementes führen. Dieses Verhalten ist bereits von Kegel- und Stirnpressverbindungen bekannt und kann zum Versagen der Verbindung führen.
Deshalb sollen Zusammenhänge zwischen Geometrie-Daten, Montage- und übertragbaren Kräften unter Berücksichtigung verschiedener Werkstoffpaarungen gefunden werden und experimentell bestätigt werden. Aus den Ergebnissen werden Auslegungs- und Konstruktionsrichtlinien abgeleitet, die eine prozesssichere Dimensionierung und Gestaltung ermöglichen und damit zu einer weiteren Verbreitung gerändelter Kegel-pressverbindungen beitragen.
Vorbetrachtungen
Am Institut für Konstruktionstechnik und Technisches Design wurden Probenkörper bestehend aus Stahlwellen mit gerändeltem Kegelprofil und Naben aus verschiedenen Werkstoffen gefertigt (Bild 2). Die Wellen wurden im Bereich des Kegels mit einem Rändelprofil entsprechend [DIN82] versehen. Die Naben aus Stahl, Aluminium und Plexiglas verfügten über eine kegelförmige Innenkontur ohne Rändelung. Diese sollte sich beim axialen Aufpressen bilden.
In Bild 3 sind mehrere Versuche zum Aufpressen von Probenkörpern nach Bild 2 gegenübergestellt. Um einen definierten Aufschubweg zu realisieren, streut das hierfür erforderliche Anzugsmoment deutlich. Damit ist bei Kurve "P3" ein 64% höheres Anzugsmoment nötig als bei Kurve "P1". Auf Grund dieser starken Streuungen ist ein drehmomentgesteuertes Anziehen der Verbindung als kritisch zu bewerten. Durch ein weggeregeltes Aufpressen der Nabe auf die Welle erscheint ein sicheres Anziehen der Verbindung jedoch möglich.
Zusammenfassung
Gerändelte Kegelpressverbindungen finden schon seit langem im industriellen Einsatz Verwendung, obwohl ihre Funktionsweise bislang nicht systematisch untersucht wurde. Auf Basis gängiger systematischer Einteilungen lassen sie sich gegen andere Formen von Welle-Nabe-Verbindungen abgrenzen, wobei die Auslegungsgrundlagen für diese Verbindungsarten nicht auf gerändelte Kegelpressverbindungen übertragbar sind oder ebenfalls Forschungsdefizite aufweisen.
Zukünftig sollen die bestehenden Wissenslücken beseitigt und der Einsatz gerändelter Kegelpressverbindungen durch Auslegungs- und Konstruktionsrichtlinien erleichtern und sicherer gemacht machen. Hierzu soll zum einen der Fügeprozess betrachtet und zum anderen das Übertragungsverhalten am Institut untersucht werden.
Ansprechpartner
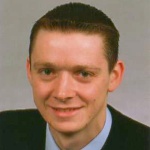
Markus Wagner
Dr.-Ing.Gruppenleiter Rechnerunterstützte Produktentwicklung