Das Projekt Rückführung von Erprobungswissen in die Produktentwicklung (RePro) wird im Rahmen einer Industriekooperation durchgeführt. Ziel ist es das Wissen, welches während Dauerlauferprobungen auf Prüfständen gewonnen wird effektiver und effizienter zu nutzen, um Fehler schneller zu erkennen und in Zukunft zu vermeiden.
Motivation
Konstruieren ist in erster Linie ein informationsverarbeitender Prozess [Hubka76, S. 7]. Der Produktentwickler legt unmittelbar Merkmale fest, während sich Eigenschaften des Produkts, welche das Verhalten des Produkts beschreiben, mittelbar ergeben. [Weber01, S. 37]. Produkteigenschaften werden in frühen Phasen des Produktlebenslaufs am stärksten beeinflusst, die Erkenntnismöglichkeit über diese Eigenschaften ist aber am geringsten; das Paradoxon der Konstruktion [Ehrlenspiel13, S. 202]. Der Produktentwickler benötigt Rückmeldungen von Informationen über Produkteigenschaften die später auf den Kunden wirken um die Auswirkungen seiner festgelegten Merkmale auf diese Eigenschaften analysieren zu können, vgl. z. B. [Ehrlenspiel13, S. 202]. Die Ermittlung von Eigenschaften erfolgt über unterschiedlichste Methoden z. B. Simulationen oder Versuche [Lindemann09, S. 157 ff.], also aus der Erprobung des Produkts.
Die Informationen aus der Erprobung müssen dem Produktentwickler rückgeführt werden. Schwachstellen und Fehler bilden wesentliche Informationen, die aus Erprobungen erhoben werden können [Lindemann09, S. 158 ff.]. Nicht behobene Fehler oder falsche Maßnahmen zu Fehlerabstellung führen zu Fehlerfortpflanzung. Die Auswirkung von später entdeckten Fehlern auf die Kosten für die Fehlerabstellung lässt sich durch die Zehnerregel (Rules of ten) beschreiben, z. B. [Reinhart96]. Der effektivere Informationsrückfluss und die einheitliche Dokumentation sollen eine effizientere Fehleranalyse ermöglichen und Folgefehler vermeiden. Diese einheitliche Dokumentation kann beim nächsten gleichen Fehler zur Analyse aufbereitet und als Vorwissen zur Verfügung gestellt werden.
Problemstellung
Der Erfahrungsschatz aus abgeschlossenen Projekten wird in der Praxis leider kaum dokumentiert [Lindemann09, S. 203]. Diese These wird durch eine beispielhafte Untersuchung der Dokumentation von Fehlerereignissen während der Dauerlauferprobung in der Fahrzeugindustrie bestätigt, wonach ca. ein Fünftel der detektierten Fehler nicht so eindeutig dokumentiert wurden, dass eine rasche Nachvollziehbarkeit gegeben war [Schenk12, S. 435 ff.].
Die Komplexität der Produkte und auch der Erprobungsmethoden steigt. Die Anzahl der Messsignale, welche beispielhaft auf Dauerlaufprüfständen aufgezeichnet und zur Fehleranalyse herangezogen werden müssen liegt bei über 2000 Signalen [Schenk13, S. 45]. Die Beherrschung der Komplexität bei der Fehleranalyse für den Versuchsingenieur und die Dokumentation aller Informationen dieser Analyse zur Rückführung in die Produktentwicklung ist methodisch und anwendungsnah zu unterstützen. Damit können eine effizientere Nutzung der Prüfstände und eine effektivere Nutzung der erhobenen Informationen gelingen
Zielsetzung
Der Erfahrungsschatz aus abgeschlossenen Projekten wird in der Praxis leider kaum dokumentiert [Lindemann09, S. 203]. Diese These wird durch eine beispielhafte Untersuchung der Dokumentation von Fehlerereignissen während der Dauerlauferprobung in der Fahrzeugindustrie bestätigt, wonach ca. ein Fünftel der detektierten Fehler nicht so eindeutig dokumentiert wurden, dass eine rasche Nachvollziehbarkeit gegeben war [Schenk12, S. 435 ff.].
Die Komplexität der Produkte und auch der Erprobungsmethoden steigt. Die Anzahl der Messsignale, welche beispielhaft auf Dauerlaufprüfständen aufgezeichnet und zur Fehleranalyse herangezogen werden müssen liegt bei über 2000 Signalen [Schenk13, S. 45]. Die Beherrschung der Komplexität bei der Fehleranalyse für den Versuchsingenieur und die Dokumentation aller Informationen dieser Analyse zur Rückführung in die Produktentwicklung ist methodisch und anwendungsnah zu unterstützen. Damit können eine effizientere Nutzung der Prüfstände und eine effektivere Nutzung der erhobenen Informationen gelingen.
Bisherige Ergebnisse
Moderne Vorgabearten und Erprobungsmethoden ermöglichen eine situationsabhängige Reaktion auf das Prüflingsverhalten. Schenk [Schenk12, S. 429 ff.] konnte zeigen, dass durch deren Anwendung eine Reduzierung und Vermeidung von Fehlern bzw. Reklamationen möglich ist. Eine reduzierte Fehlerzahl führt zu kürzeren realen Prüfstandsbelegzeiten und folglich zu effizienteren Dauerläufen (vgl. Bild 1).
Speziell unter Erprobungswissen versteht man Wissen, das für eine erfolgreiche Durchführung des Erprobungsprozesses als Grundlage vorausgesetzt wird und Wissen, das während der Erprobung gewonnen wird (vgl. Bild 2). Diese Definition von Erprobungswissen schließt sich der Definition von Konstruktionswissen nach [Koller90, S. 85] an [Karthaus13].
Informationen und Wissen müssen aus dem Erprobungsprozess und dem Testobjekt mit dem diese Erprobung durchgeführt wurde in die Entwicklung rückgeführt werden (siehe Bild 3). Diese Rückführung muss für eine effiziente Nutzung des Erprobungswissens, der gesammelten Daten und Informationen und auch der erlernten Erfahrungen methodisch unterstützt werden und soll so zu einer Produktverbesserung führen.
Literatur
Ehrlenspiel13 | Ehrlenspiel, K.; Meerkamm, H.: Integrierte Produktentwicklung Denkabläufe, Methodeneinsatz, Zusammenarbeit. München Wien: Carl Hanser Verlag, 2013. |
Hubka76 | Hubka, V.: Theorie der Konstruktionsprozesse Analyse der Konstruktionstätigkeit. Berlin Heidelberg New York: Springer Verlag, 1976. |
Karthaus13 | Karthaus, C.; Schenk, M.; Klos, W.; Binz, H.; Bertsche, B.: Automatisierte Fehlerreaktion und lernfähige Fehleranalyse zur Erhebung von Erprobungswissen auf Antriebstrangprüfständen. In: Spath, D.; Bertsche, B.; Binz, H. (Hrsg.): Stuttgarter Symposium für Produktentwicklung 2013. Stuttgart, 2013. |
Koller90 | Koller, R., Berns, S.: Strukturierung von Konstruktionswissen. In: Konstruktion 42 (1990), Nr. 42, S. 85-89. |
Lindemann09 | Lindemann, U.: Methodische Entwicklung technischer Produkte. Dordrecht Heidelberg London New York; Springer Verlag, 2009. |
Reinhart96 | Reinhart, G.; Lindemann, U.; Heinzl, J.: Qualitätsmanagement. Berlin Heidelberg New York; Springer Verlag, 1996. |
Schenk12 | Schenk, M.; Klos, W.; Karthaus, C.; Binz, H.; Bertsche, B.: Effizienzsteigerung bei der Antriebsstrangerprobung durch Einsatz moderner Erprobungsmethoden und Optimierung der Fehleranalyse. In: VDI-Berichte 2169, VDI Wissensforum GmbH (Hrsg.): 16. Berechnung, Simulation und Erprobung im Fahrzeugbau 2012. Baden-Baden, 2012, S. 429-440. |
Schenk13 | Schenk, M.; Behrendt, H.; Klos, W.; Karthaus, C.; Binz, H.; Bertsche, B.: Automatisierte Fehlerreaktion am Antriebstrangprüfstand. In: Christ, C.; Beidl, C. (Hrsg.): Beiträge 5. Internationales Symposium für Entwicklungsmethodik. Wiesbaden, 2013, S. 40-55. |
Weber01 | Weber, C.; Werner, H.: Schlussforderungen für Design for X aus der Perspektive eines neuen Ansatzes zur Modellierung von Produkten und Produktentwicklungsprozessen. In: Meerkamm, H., (Hrsg.): Design for X: Beiträge zum 12. Symposium. Neukirchen, 2001, S. 37-48. |
Zeller90 | Zeller, P., Sonntag, E.: Rechnerintegriertes Informations- und Testsystem in der BMW Antriebsentwicklung. In: ATZ 92 (1990), Nr. 9, S. 516-524. |
Partner
Das Forschungsprojekt wird im Rahmen einer Kooperation mit dem Powertrain Prüffeld der DAIMLER AG in Untertürkheim durchgeführt.
Ansprechpartner
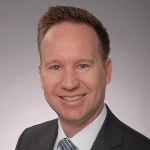
Daniel Roth
Dr.-Ing.Leiter Finanzen und Verwaltung;
Stlv. Leiter Konstruktionstechnik;
Gruppenleiter Methodische Produktentwicklung